Digital Journal HVAC Press Release
7081030452 • April 23, 2025
Unmatched Expertise in Comfort: Guaranteed Air Pro Mechanical, the Premier HVAC Contractor in Norman, OK
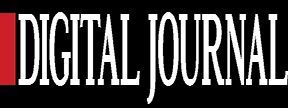
PRESS RELEASE
Published March 19, 2024
Norman, OK - In the dynamic world of heating, ventilation, and air conditioning (HVAC) services, Guaranteed Air Pro Mechanical stands out as a leader in providing exceptional service in Norman, Oklahoma, and its surrounding areas. As a trusted HVAC contractor, the company has carved a niche for itself by offering comprehensive HVAC solutions, including installations, maintenance, and repairs, tailored to meet the unique needs of each client.
With over eight years of dedicated service in the industry, Guaranteed Air Pro Mechanical has developed a reputation for precision and reliability. The team's expertise in handling various HVAC systems ensures that clients receive only the best in terms of efficiency and functionality. Whether it's a sweltering summer day or a chilly winter night, Guaranteed Air Pro Mechanical guarantees the comfort of its customers throughout the year.
The company's services are not just limited to Norman. The team has expanded its reach to include Moore, Noble, Yukon, Edmond, Goldsby, Purcell, Del City, Blanchard, Newcastle, Midwest City, and Oklahoma City. Moreover, they are now growing their presence in Broken Arrow, Lawton, Enid, Stillwater, and Muskogee. This expansion signifies their commitment to bringing top-quality HVAC services to a broader audience.
One of the key differentiators for Guaranteed Air Pro Mechanical is its competitive pricing model. Understanding the financial constraints that often accompany HVAC services, the company has devised pricing strategies that ensure affordability without compromising on the quality of service. This approach has garnered them a loyal customer base who value both quality and affordability.
Clients who choose the HVAC contractor Norman can expect a seamless experience from start to finish. The team's meticulous approach to installations ensures that each system is set up for optimal performance. Regular maintenance checks are conducted to prolong the lifespan of the HVAC systems and prevent any unforeseen breakdowns. In cases of repairs, the skilled technicians at Guaranteed Air Pro Mechanical are skilled at diagnosing issues quickly and resolving them efficiently, minimizing downtime and inconvenience for the clients.
One of the hallmarks of Guaranteed Air Pro Mechanical is its prompt and timely service. Recognizing the urgency often accompanying HVAC issues, the team ensures swift response times, thereby reducing inconvenience and discomfort for its clients. This responsiveness, coupled with their commitment to quality, makes them stand out in a competitive market.
About Guaranteed Air Pro Mechanical:
Guaranteed Air Pro Mechanical, based in Norman, OK, is a premier HVAC contractor with over eight years of experience in the industry. Offering a range of services, including installations, maintenance, and repairs, the team is known for its precision, efficiency, and customer-centric approach. Serving a wide area that includes Norman, Moore, Noble, Yukon, Edmond, Goldsby, Purcell, Del City, Blanchard, Newcastle, Midwest City, Oklahoma City, Broken Arrow, Lawton, Enid, Stillwater, and Muskogee, they are committed to ensuring the comfort and satisfaction of their clients. With competitive pricing and a team of skilled technicians, Guaranteed Air Pro Mechanical is the ideal choice for all HVAC needs.
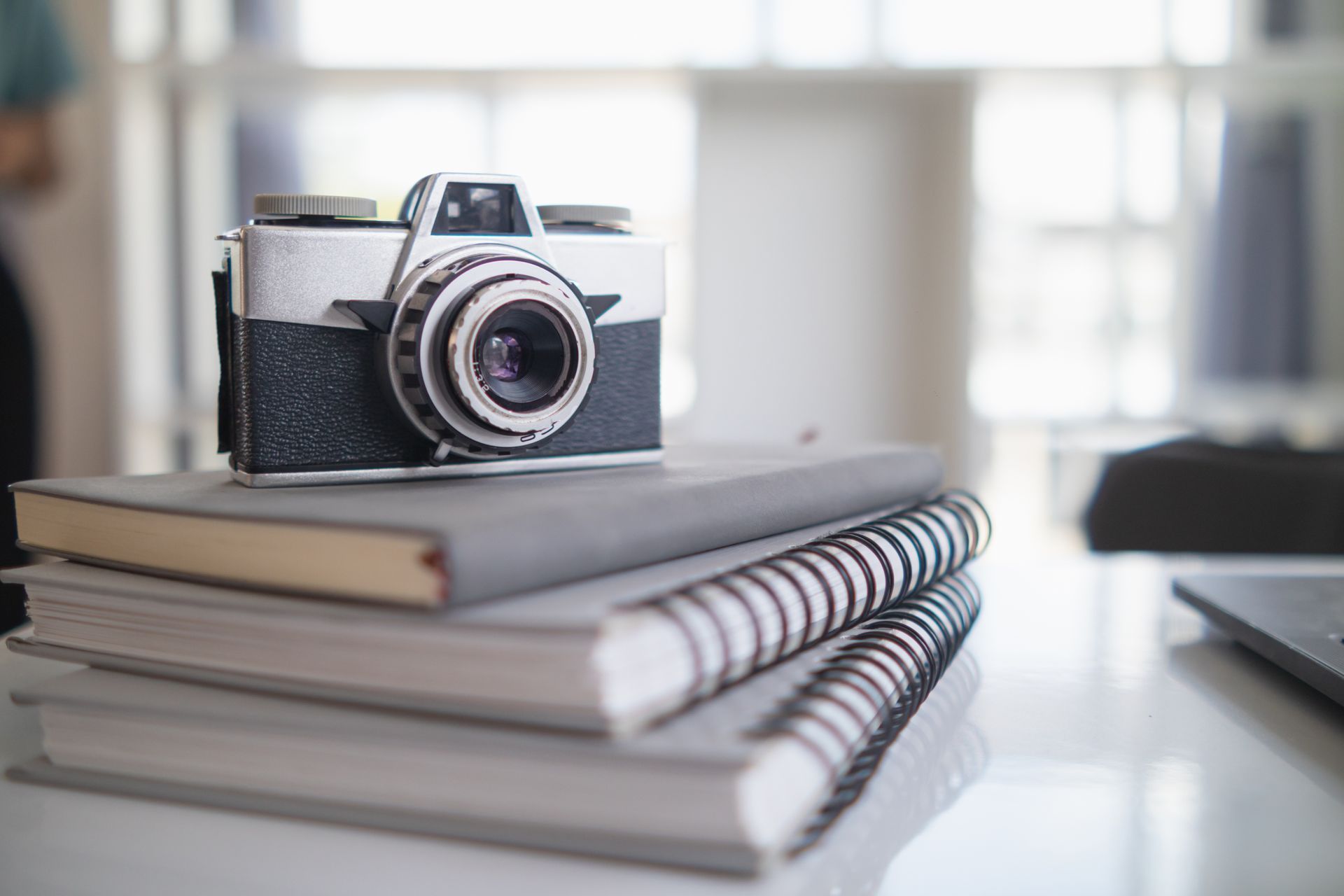
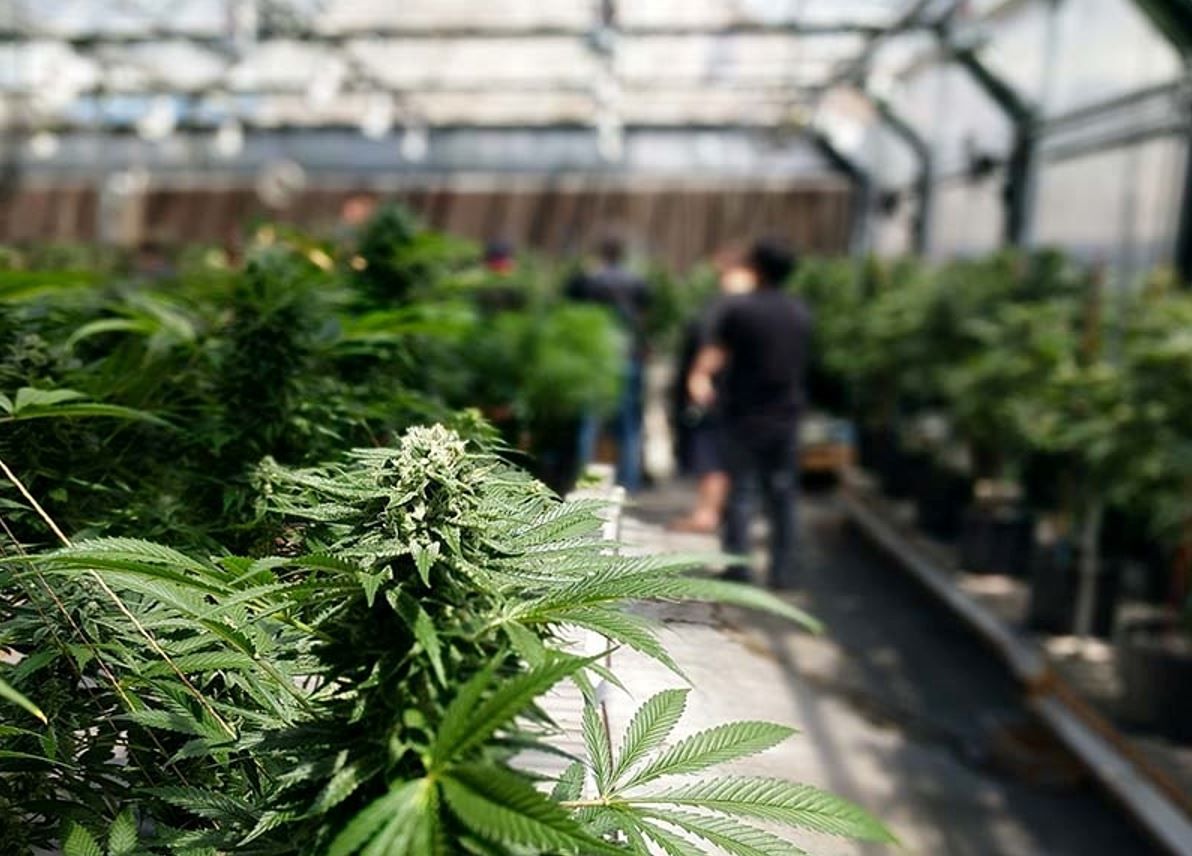
Cannabis grow facilities offer HVAC requirements and pitfalls unlike just about any other application, and Angelo Tomarchio brings an unusually strong pedigree to the grow facility projects he works on. Tomarchio’s father and grandfather farmed their own land. Tomarchio offers his own strong background in HVAC, where he now serves as owner of Guaranteed Air Pro Mechanical in Norman OK. But in between, Tomarchio also owned and operated his own grow facility with a partner. The time demands eventually led the partners to sell the business. However, Tomarchio’s varied experience has helped him develop cannabis-related business into roughly one-third of G.A.P.'s business mix. On the contractor side, Tomarchio has overseen HVAC for projects ranging from a small 400-sq-ft room to, more recently, a 60,000-square-foot building. Ask Tomarchio about grow facility particulars that HVAC contractors should know about, and he is ready with examples. O2, CO2, and You Outside air is not a novel concept. It’s a building code staple. Nevertheless, a lot of growers don’t want any outside air, Tomarchio said. So that can mean a conversation about the benefits of fresh air. Tomarchio then pursues the goals of cultivation, fresh air, and exhaust. In this environment, mechanically bringing in CO2 is desirable while still “scrubbing” the room with fresh air. “Within that realm, we were designing things a little differently,” he said. “Carbon monoxide hangs low in the atmosphere. So if you are going to pull in fresh air, we recommend that you pull it in low,” he began. “Then you exhaust up high, so that literally your trunk run would run the full length of the building on one side. And supply holes, ported out, coming out underneath the canopy of the marijuana. And then it would exhaust on the opposite side, up high, at the roofline.” That solution creates another problem: introducing CO2 into the space necessitates an emergency setup for evacuation. “So now, you're splitting your exhaust where you've got a point up high, and you're breaking that leg and putting a damper system and dropping another pipe down onto the ground,” Tomarchio said, “because you have to be at least 12 inches or lower on the ground for the intake for CO2 evacuation.” In one way, the system now entails three different systems — or maybe just two: one for occupancy and one for CO2, if the owner is adamant in skipping outdoor air. All-In One Advances Equipment is evolving to meet the menu of demands for grow facilities, and contractors could do countless residential or commercial jobs without ever needing to see it. These units can attack dehumidification, heat or air conditioning as the moment requires, and outside air needs. The high-end combo equipment is made more specifically for a horticultural or laboratory area. Tomarchio explained that these units may include “fresh air intake loops that you can add, that are controlled by a damper to pull in fresh air to qualify for your occupancy” needs, while also offering higher filtration than a standard package unit. The equipment can also compensate for one of a cannabis grow facility’s most unusual demands: needing to run the air conditioner when it’s 15°F outside. “Now they have low ambient controls, so it will adjust the motors, the compressors, and the fans to cool that area as if it was a 90° day outside when it's 15° or lower. And still get a full capacity on your Btus.” Water Cooling Meets the Laws of Nature With that, a contractor has theoretically conquered ventilation needs, a CO2 component, and how to cool a grow room in a blizzard. What could possibly be left to deal with? “Now you’ve got a drain line,” Tomarchio observed, for a packaged unit outside, and when the system is cooling in subzero temps, it contains condensate that is waiting to freeze up. A system might also have an inside condenser or inside air handlers that are draining outside, he noted. “You have to add some kind of heating rope or heating element to the line.” Tomarchio has seen drain lines freeze during severe cold despite the benefits of insulation and heater tape. Defrost sticks like ones used in walk-in refrigeration can work, he said, but in order to wrap around the line, they require 220 V plugs outside. Not many facilities will have been designed with that capacity. In that case, a contractor may be left trying to cut the drain line, put the brand new line on, wrap it with a 110 V heat strip, and/or insulate it with ¾-inch Armaflex, Tomarchio said. In a pinch, cutting off the line right at the wall and then sticking a piece of string in the drain line has worked. “That water will follow that string, creating a little drip-down with an icicle,” he explained. “But that, too, will only last so long.” It might get a facility through a week of exceptionally steady cold, though, even if someone may need to occasionally go outside with a hammer and tap to try to knock some ice out. It's a Jungle In There Of course, this chain of grow-specific challenges and solutions is just the tip of the iceberg for proper HVAC installation and maintenance in these spaces. Humidity control remains a critical task. Dehumidification may get more attention, but Tomarchio will walk a listener through the why’s and how’s of keeping both temperature and humidity a bit higher at stages than conventional wisdom might suggest. “This is probably more of the grower in me talking, but good marijuana is usually a jungle-type plant,” he said. “It likes some high temperatures, and it likes humidity. It’s a weed. You know the grass that's growing in your sidewalk when it's wet, and hot and humid? It’s kind of the same thing, especially in the vegetative state.” So where growers commonly set temperatures at 80°F, Tomarchio prefers 85 up toward 90. After all, he argues, there are 90° days outside, so as long as water and humidity are adequate “and you’re not killing them with your lights, you can replicate that into a controlled indoor environment.” Contractors in this space would need familiarity with simple portable oxygen concentrator (POC) humidifiers, but also with the pros and cons of steam humidification, too, as the next step up. Not content with available options, Tomarchio has designed a unit for some of G.A.P.'s projects. It combines ultrasonic mist with disc technology like that used in humidors and settings with similar needs. He likes its ability to deliver superfine mist without getting “drippy” like some units and without other units’ occasional calcification or “burping” water on the floor. Tomarchio combats “Hey, bro science” when non-professionals offer a client low-context advice like, “Hey, bro, you should get your grow room’s humidity down to 40%.” Clients and Competition In Guaranteed Air Pro's market, Tomarchio sees the customer base for cannabis grow facilities getting larger these days. Potential clients are also better informed and more serious, on the whole, than some guy looking to “throw up quick garage setups.” Some customers who may have started with little experience have done well in the business and gotten smarter along the way. Tomarchio has seen some of them start with a small room, then build out another 3,000-square-foot room. And then another 3,000 square feet, and then another. But others can still roll in espousing what Tomarchio calls “‘Hey, bro’ science.” That happens after the client has a conversation with someone whose bright idea is uninformed or lacks context. Maybe a client was talking about strategies in a shop or online community and someone told them, “Hey, bro, you should get your grow room’s humidity down to 40%.” Tomarchio offers consulting services in addition to contracting, in part for situations like that. This is not only useful for some customers in achieving a better design, but for the sake of both G.A.P. and the client, it can nip a variety of potential technical and contractual issues in the bud before installation gets going. Tomarchio expects a market bubble to develop and work itself out. Those bubbles always attract some contractors looking to make a quick buck, too. G.A.P. Mechanical has benefited from a number of projects where a grower had a terrible experience and hires Tomarchio to come in and deal with the HVAC mess. Looking beyond the quick buck has served G.A.P. well so far. “I want the contract,” said Tomarchio. “I tell them, ‘Hey, I want to see you every three months, want to come in here and maintain these machines and clean them all and test them all, and run them through diagnostics and make sure there's no issues going on.’” “If there is an issue, what can we do? Nobody's perfect. I might put an extra bend in the pipe, which lowered my back pressure on the pipe, and now one part of the room was a little bit warmer or colder. You know, okay, how do we adjust that one little section there?” In this sector, successful clients and knowledgeable HVAC contractors can still find room to grow. By Robert Beverly- the NEWS
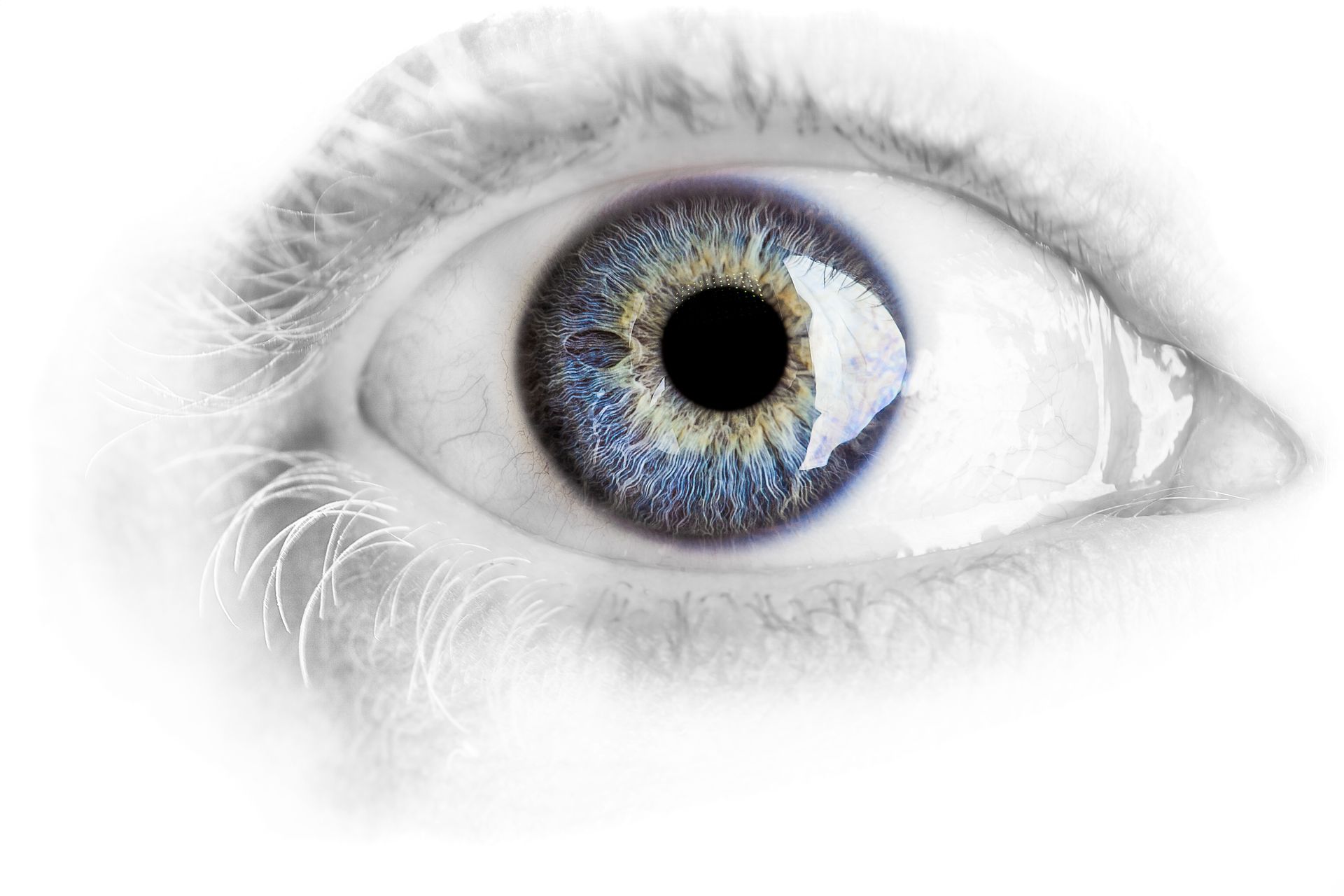
Our AC and Heat clients always have a habit of wanting to watch us work or repair there HVAC system. Its very common occurrence and I believe it is a symptom of trust that leads to the intrigue. There are many trade videos comedic sketches, and even shirts that look at this occurrence in the HVAC field, and yes, they all favor the AC technician. Its not personal its just funny. At Guaranteed Air Pro we encourage you to watch and ask questions as long as your safety is not a concern. Lets take a look at a story that I relate to when it comes to this exact situation but has nothing to do with a heat and air system. . Elliot had never liked people looking over his shoulder. Whether it was typing an email, sketching in his notebook, or even just scrolling through his phone, he always felt exposed, like someone was peering into his thoughts. That changed when he met Sam. Sam was the kind of person who never hesitated to lean in, glance at what Elliot was doing, and ask questions. At first, Elliot found it irritating. “Give me some space,” he’d say, shifting away slightly. But Sam would just smile. “If there’s nothing to hide, why does it bother you?” That question stuck with Elliot. It wasn’t about privacy—he had nothing secretive on his screen, no hidden messages or double meanings in his words. But there was a discomfort in being seen so openly. One afternoon, as Elliot worked on a design project, Sam once again leaned in behind him. This time, instead of tensing up, Elliot let it happen. Sam watched as he refined the lines and adjusted the colors. “That looks great,” Sam said. “I love how you’re layering the shadows.” Elliot blinked. He had expected critique, maybe even judgment. Instead, there was only appreciation. Over time, he realized that when someone looked over his shoulder, it didn’t have to mean scrutiny—it could mean trust. It could mean shared excitement. It could mean honesty. One day, Sam hesitated before looking at Elliot’s screen. “Mind if I see?” Elliot smiled. “Go ahead. Nothing to hide.” And from that moment on, he didn’t mind anymore. So in sort, ask questions, watch us repair and work. When it comes to Heat and AC we have nothing to hide.
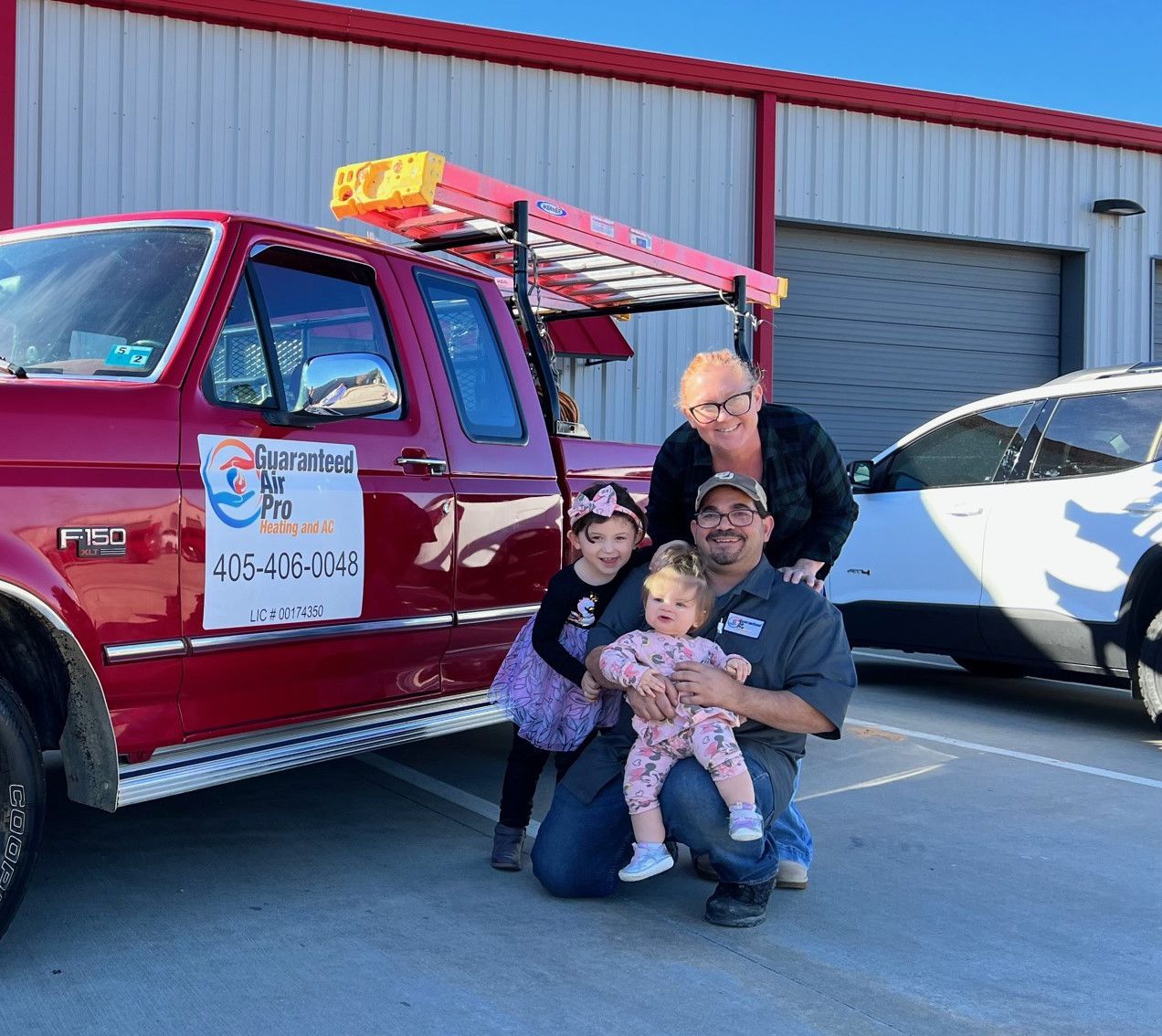
I want to take a moment to thank everyone for joining and being part of this journey. Instead of running a traditional blog that just shares industry news and tips, I’m taking an unconventional approach. My goal is to use this space to gain real insight—not just into the HVAC world, but also into my company, Guaranteed Air Pro Mechanical, and the amazing people behind it. Rather than just posting general information, I’ll be diving into the experiences, challenges, and innovations that shape our work. I want to explore the personal stories of our team members, the unique design choices we make, and the creative ways we approach HVAC solutions. This blog isn’t just about technical know-how; it’s about showcasing what makes us different and the passion we bring to every project. My name is Angelo Tomarchio. I am a Oklahoma transplant that grew up in New Jersey on a large family vegetable farm. Then made my way to New Mexico and work in the Art Department for the film industry. To present owner-operator of Guaranteed Air Pro. As a young kid, 10-15YR old, in the fields of New Jersey-yes it is called the garden state and yes there are a number of farms there- I started out with my first family summer job, moving burlap potato sack filled with 52 ears of NJ Sweet Corn in to trucks, trailers, and vans. When involved in farm operation you gain a quick education in solving complicated problems and all the trade skills that are utilized when resoling these issues. This was the beginning of my mechanical career until the age of 18. My father never wanted me to be a farmer even with a plot of land in excess of 200 acres still farmed today. I left NJ to attend college in Santa Fe NM in the field of film production with a concentration on set building and architectural/figurative sculpture. I had the pleasure of working for MGM, DreamWorks, Disney, Paramount, HBO, and many others for 16 years. I then meant my beautiful wife Amy Marsh whom grew up in Norman, Oklahoma, and with that we decided to take roots in Norman and have 2 amazing daughters, Amelia- currently 11YR, and Annabella- currently 3YR old. I started working in general contracting around the state and then joined with a family member operating my first HVAC company. I graduated HVAC trade school and went on to become a Mechanical Journeyman and then a Mechanical Contractor. Unfortunately the partnership did not workout even after many accomplished, long working years and ultimately lead to the creation of Guaranteed Air Pro. It has since been a pleasure to build our brand and allow our customers to become part of the GAP HVAC family. I hope our growing small business, located in the great city of Norman Oklahoma will continue to grow, while focusing on providing a hard work ethic, transparency, honesty, professionalism, and HVAC knowledge for all our GAP members for many years to come. By opening up this conversation, I hope to connect with professionals, customers, and enthusiasts who appreciate fresh perspectives. Let’s build something unique together—so feel free to share your thoughts, ask questions, and be part of the discussion. Contact us at Info@GAPACOK.com . Thanks again for being here, and I look forward to growing this community with you!